The supply chain partner for sexual and reproductive health and rights
UNFPA is the lead agency within the United Nations system for the procurement of sexual and reproductive health (SRH) supplies and the world’s largest public-sector procurer of contraceptives. We leverage the significant volume of contraceptives procured annually to secure cost-effective, quality products to meet global needs.
The UNFPA Supply Chain Management Unit (SCMU) provides the organization with a responsive and resilient supply chain system across development and humanitarian settings. The SCMU delivers coordination and oversight of all UNFPA supply chain-related activities to reach women and adolescents and expand equitable access to affordable, quality-assured SRH products and services.
Access to safe, voluntary family planning is a human right. Few things have a greater impact on the life of a woman than the number and spacing of her children. Family planning is central to gender equality and women’s empowerment, and it is a key factor in reducing poverty. One measure of access to sexual and reproductive health services is the extent to which a woman who wants to use a method of contraception has access to it.
UNFPA delivers supplies to UNFPA programmes and partners in over 150 countries, managing a global supply chain that responds to the needs of partners in development. UNFPA partners with governments and non-governmental organizations (NGOs) to access UNFPA’s expertise and purchasing power to best make use of domestic resources and donor funds to procure supplies.
Humanitarian response procurement
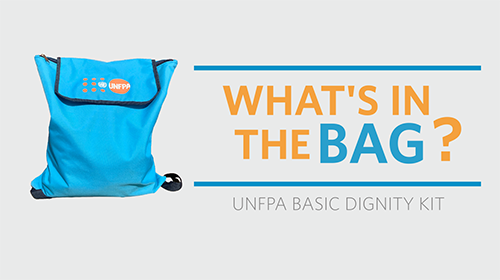
UNFPA moves quickly when emergency strikes to protect the reproductive health of communities in crisis. In support of The Minimum Initial Service Package for Sexual & Reproductive Health, UNFPA keeps 13 different Inter-Agency Reproductive Health (IARH) Kits and a range of complementary commodities in stock for urgent and emergency requests. The IARH kits are designed for specific health service delivery levels and for specific population sizes for a period of 3 months.
UNFPA also maintains stock of basic Dignity Kits. The kits help women and girls maintain proper hygiene after being displaced and are a critical component of the UNFPA humanitarian response.
The basic kit contains 10 key essential supplies and can be delivered within 48 hours. Dignity Kits can also be customized with 39 different items.
Whether working in sexual and reproductive health, family planning, humanitarian response or census, UNFPA delivers quality supplies in a cost-effective and reliable way.
For more information, see the resources below or contact us.
Access to safe and effective contraceptives, medicines and equipment
UNFPA procures quality assured products including condoms, IUDs, medical devices & equipment, hormonal contraceptives, and medicines to support maternal, sexual and reproductive health.
UNFPA evaluates and prequalifies suppliers based on internationally recognized quality standards before entering into contractual agreements. UNFPA quality assurance activities follow a systematic process to ensure that products meet specified requirements and standards. Quality assurance activities include prequalification, technical evaluations, quality control, and monitoring. Quality control activities determine whether the specified standards are being maintained through inspection, sampling, and laboratory testing.
Please refer to the UNFPA Quality Assurance Framework for more detailed information.
Medicines
The UNFPA Quality Assurance system aligns with United Nations partner agencies. Following international quality standards and supported by the World Health Organization (WHO) and other organizations, UNFPA has defined a quality assurance policy for hormonal contraceptives and other medicines. The highest importance is given to the prequalification process. To prevent an interrupted supply of medicines under the WHO Prequalification Programme, an interim process called the Expert Review Panel (ERP) is available when fewer than three prequalified products are offered. The ERP is for manufacturers on their way to – but have yet to achieve – prequalification status. Results of the latest ERP process conducted are available here.
UNFPA evaluates and implements quality control measures for medicines not under WHO Prequalification or ERP assessment in accordance with good practices. This quality evaluation will be based on Good Manufacturing Practice (GMP) compliance and applicable technical documentation reviewed and approved by an internal technical committee.
Medical Devices
Medical devices and equipment are vital in the screening, prevention, treatment and management of illnesses, diseases and health interventions. UNFPA follows recommendations on standards and quality systems for medical devices set by the WHO and the International Medical Device Regulators Forum (IMDRF) to prevent the supply and use of substandard and falsified devices and equipment and safeguard public health and safety.
Capacity building
UNFPA offers capacity strengthening in the form of technical support, training, and mentoring activities for key stakeholders in the production and regulation of sexual and reproductive health commodities.
Joint WHO-UNICEF-UNFPA Meeting for Manufacturers and Suppliers
The registration is open to the UNICEF, UNFPA and WHO meeting for manufacturers and suppliers in UN City Copenhagen on 2-6 December 2024.
This year’s theme is: Ensuring Health Equity: Partnerships For Accessible Quality Products.
Environmental Strategy
The goal of the United Nations is to become climate neutral and environmentally sustainable, as described on the Greening the Blue initiative’s website.
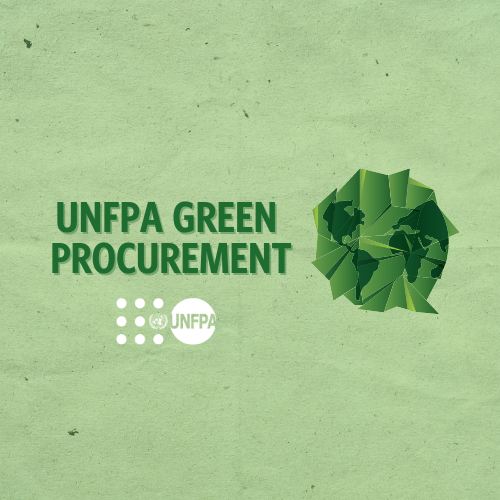
The UNFPA Green Procurement Strategy outlines the environmental focus areas for which UNFPA has instituted requirements toward sustainability and the process through which suppliers are expected to demonstrate they meet these requirements. To make improvements, suppliers can exercise influence in four parts of their organization: at site level, supply chain, products and packaging.
Safe disposal of reproductive health commodities is critical as consequences of improper and unsafe disposal pose public health and environmental implications. UNFPA has developed a guidance document on responsible management and safe disposal of unusable by-products of UNFPA procured commodities.The Safe Disposal and Management of Unused, Unwanted Contraceptives provides recommendations on policies and procedures. The guideline should be useful for situations where commodities are expired, counterfeit, have quality issues or are unused for various reasons.
Social responsibility
UNFPA supports and encourages suppliers to participate in the UN Global Compact, a voluntary initiative covering human rights, labor rights and the environment. Suppliers must comply with the UNFPA General Conditions of Contract, which contain specific provisions regarding child labor, mines and sexual exploitation.
Ensuring that supplies reach the last mile
Since 2018, UNFPA delivered programme supplies worth USD 472.5 million in more than 114 countries. Among these were male and female condoms, oral and injectable contraceptives, intrauterine devices (IUDs), maternal health and life-saving supplies, medical equipment, reproductive health,dignity kits and PPE (Personal Protective Equipment).
In order for UNFPA to achieve its transformative goals of eliminating the unmet need for family planning and ending preventable maternal deaths, it is vital to ensure that these supplies reach the women and girls UNFPA serves on time. To that purpose, in 2018 UNFPA launched a corporate-wide initiative called the Last Mile Assurance (LMA) process.
The LMA process aims to monitor and strengthen the supply chain used to safeguard and distribute these essential reproductive health supplies, through a multifaceted approach that allows UNFPA to:
- Increase its visibility of the adequate safeguarding, management, and use for intended purposes of family planning, maternal health, and other programme supplies UNFPA provides.
- Holistically quantify actual fiduciary and delivery risk, to allow for improved programming and better discharge fiduciary duty to the donors that provide the financial resources used to procure the supplies.
- Help UNFPA partners to better manage the programme supplies entrusted to them, by identifying supply chain capacity gaps, preventing fraud, and minimizing waste and losses.
- Enforce accountability for the safeguarding, management, and use of the supplies by UNFPA partners.
How is this done?
The LMA process ensures that supplies reach the last mile through the utilization of five different tools: supply chain maps, supply chain management capacity and risk assessments, programme supplies report, and finally, spot-checks and audits.
The LMA process builds on agreements signed with all implementing partners which clearly outline the terms and conditions under which the partners must manage, safeguard and distribute the supplies.
Development of supply chain maps is the first step in the LMA Process. The supply chain maps provide UNFPA with an initial level of visibility of key components of the partners’ supply chain at the national, subnational, and local levels. As they are updated on an annual basis, UNFPA can easily see the physical flow of UNFPA programme supplies and corresponding information flows.
Supply chain management capacity assessments allow UNFPA to identify the strengths and weaknesses of implementing partners in a large realm of relevant supply-chain management areas, and identify measures to improve their performance.
Supply chain management risk assessments are used to assess the risk inherent to the handling and distribution of the supplies through a model that reflects eight relevant risk factors across three key areas: external, delivery, and fiduciary risk. Each partner is assigned a “risk score”, which objectively communicates the level of risk associated with the supplies reaching women and girls in a specific context, and determines the scope and frequency of subsequent LMA process activities.
Programme supplies reports, the fourth tool of the LMA process, provide detailed information on receipts and distributions of UNFPA programme supplies, waste and losses throughout the reporting period, and the stocks on-hand available for future distribution. This report allows UNFPA and partners to better support programmatic decisions, improve traceability of UNFPA deliveries to partners, and identify the extent of waste and losses and fraud instances.
On-site verifications (referred to as spot-checks) and independent inventory audits are performed to quantify the actual level of fiduciary and delivery risk faced in the down-stream supply chain activities. They both involve the following: tracing of deliveries and distributions down to the receiving facilities, review of inventory records, measurement of waste and losses, an inspection of facilities against a set of critical warehousing and inventory management standards, assessment of the effectiveness of inventory accounting controls, and the identification of “red flags.” These are potentially indicative of instances of product diversion or other fraud schemes that could affect the supplies donated by UNFPA.
What has our progress been?
With the data gathered from the LMA Process, UNFPA has not only gained a better understanding and greater visibility of our partners supply chains but also made the transition from gathering data to creating tangible actions for the continued strengthening of our partners. We have prevented large scale waste & losses, we have strengthened our partners supply chains and capacity, and we are even helping digitize health systems. The Last Mile Assurance Process has been central to the sustainable enhancement of our partner’s supply chains.
UNFPA catalogue
UNFPA is currently enhancing our Supply Chain online resources for optimal performance. We understand the importance of seamless service and apologize for any delays during this transition. Our team is diligently working to ensure a swift resolution. Should you have questions or need assistance to our product catalogue, please reach out to UNFPA Supply Chain Management Unit at supplychain@unfpa.org.